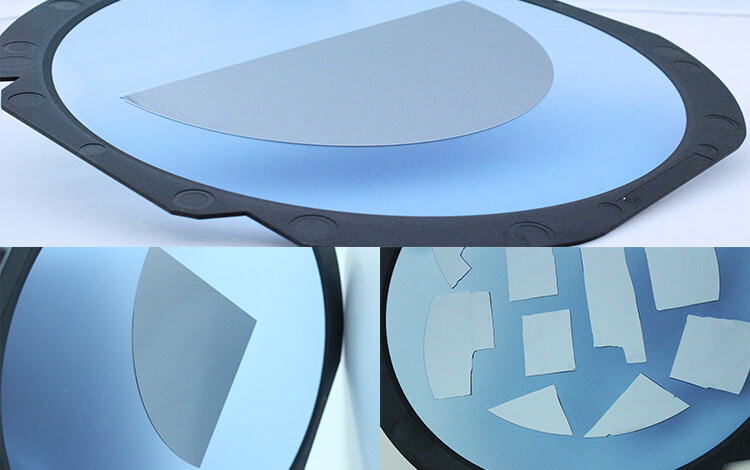
How Diamond Blades Are Made For Blade Dicing
Blade Dicing can be done on hard materials by using high diamond concentration dicing blades. Cutting edge wear is also a factor, and monitoring the process is necessary for optimum dicing quality. In addition, dicing blades need to have a long life. For this reason, it is important to check the condition of the blade regularly and change it if necessary.
High diamond concentration dicing blades are used for hard materials
High-diamond concentration dicing blades are the most durable and effective dicing blades for hard materials. They are also an excellent choice for ultra-hard and brittle materials. The higher the bond hardness, the better the retention of the diamond particles and the longer the life of the blade. There are three types of bond hardness: Soft, Medium, and Hard, with dozens of variations within each category. The bond hardness is crucial for a successful dicing operation.
Blade dicing in San Jose is available in different mesh sizes, and its use depends on the thickness of the material they cut. The thickness of the blade determines the number of diamonds they can cut and also determines the feed rate, spindle speed, and cutting depth. In addition to hard materials, high-quality diamond blades can cut sapphire and semiconductor die. The hardest workpieces, such as sapphire, often result in chipping or damage, which may reduce the yield of the product. A high-quality diamond wafering blade will provide smooth cuts, consistent performance, and a high yield.
Monitoring of dicing process is necessary
Blade dicing is an essential process in semiconductor manufacturing and requires a high degree of precision. This process requires a precise blade that is calibrated and adjusted to maintain accuracy. It is also critical to ensure that the blade is not too rigid or too loose in order to produce consistent results.
The rate at which the wafer substrate is fed into the cutting blade determines the yield and productivity of the process. The blade feed rate depends on the feed rate, blade type, and spindle speed. To maximize throughput and minimize blade damage, process engineers should select the feed rate based on these factors.
It is also important to monitor the torque of the blade. If the torque is too high, chips will form on the back side of the blade. This requires proper adjustment of the blade to prevent chipping. Taking measurements during the dressing process allows you to control the amount of time it takes and improve productivity.
Blade dicing involves multiple cuts through a wafer. The thinner the cut, the longer the blade will be exposed. As a result, the blade wear will decrease. The blade wear will affect coolant flow and the clearance between the wafer and the flange. As a result, excessive blade wear will limit the use of the blade and restrict the flow of the coolant.
The dicing blade will cut through the wafer while also removing any debris. This will create a groove in the material. The cutting blade needs to be fed at a precise rate. Therefore, special monitoring equipment will be necessary.
The laser-based blade dicing process offers many advantages over other processes. Unlike other systems, it has a high repetition rate and does not require a dressing process. A high repetition rate laser will reduce the chipping risk while minimizing tool wear.
Cutting edge wear affects dicing quality
In order to maximize the performance of dicing machines, the dicing blade should be properly mounted. Incorrect mounting can cause blade wobbling, slanted cuts, more chipping, and eventually breakage. The cutting speed is a critical factor for high-quality dicing. Different materials require different cutting speeds. For instance, harder materials require greater cutting speeds than softer ones.
Moreover, the thickness of the workpiece is a significant determinant of the chipping quality. However, TEGs and films on the front side of the wafer may negatively affect the blade’s cutting power. The backside of the wafer may also suffer from clogging, which compromises the quality of processing. However, using a step-cutting technique and a blade dicing tool that features the Short Kerf Check function can help you solve these problems and maintain a high-quality process.
Another factor that affects dicing quality is the wear of cutting edge 14. It will also create flaring protrusions on the side surfaces of the workpiece. This can cause defects in the package.
In addition to the cutting edge, the coolant concentration is also important. The amount of exposure of the dicing blade is also an important factor in dicing quality.
Long life of dicing blades
One of the most important factors that determine the cost of ownership for a dicing system is the life of the dicing blades. The blade bonding material plays a key role in the lifespan of the blade. Blades that are bonded to softer materials have a longer life, but they also wear faster than those that are hard-bonded. This tradeoff requires an evaluation of chip size and chip quality to determine the right balance.
These factors include size, shape, concentration, and bond strength. This results in a long life for dicing blades.
Another factor that affects the life of dicing blades is the coating. Resin-bonded blades are less likely to chip than metal-bonded blades. The coating prevents the blade from losing its form during the process and reduces chipping. The coatings also provide a low CoF, which inhibits blade deterioration.
The diamond-cutting surface area on a dicing blade is important. A higher diamond concentration in a cutting surface means more cutting crystals, but also a longer life. Diamonds can break at high speeds, while slower speeds may wear the diamond out prematurely. The optimum surface speed must balance these two disadvantages. Cutting at lower speeds will extend the life of a dicing blade, but the additional power used will more than offset the cost savings.
Another factor that affects dicing blades is the depth of cut. If the cutting depth is too low, radial wear will occur. A higher depth of cut means more contact time and higher dicing pressure. High-speed dicing can damage the coating, reducing the blade’s life.
The metal-bonded diamond blade is made of diamonds that are sintered into a metal matrix. The metal matrix may be copper, iron, nickel, bronze, or other metals. The metal matrix has a smooth surface, and the diamond particles are relatively large.
Thanks for visiting isposting